- Products
- Market Solutions & Services
- Insight
- Tools & Resources
- About Nexans Australia
- Search
- Contact us
- Compare
- Sign in
Thermoplastic Elastomer
Oct 27, 2021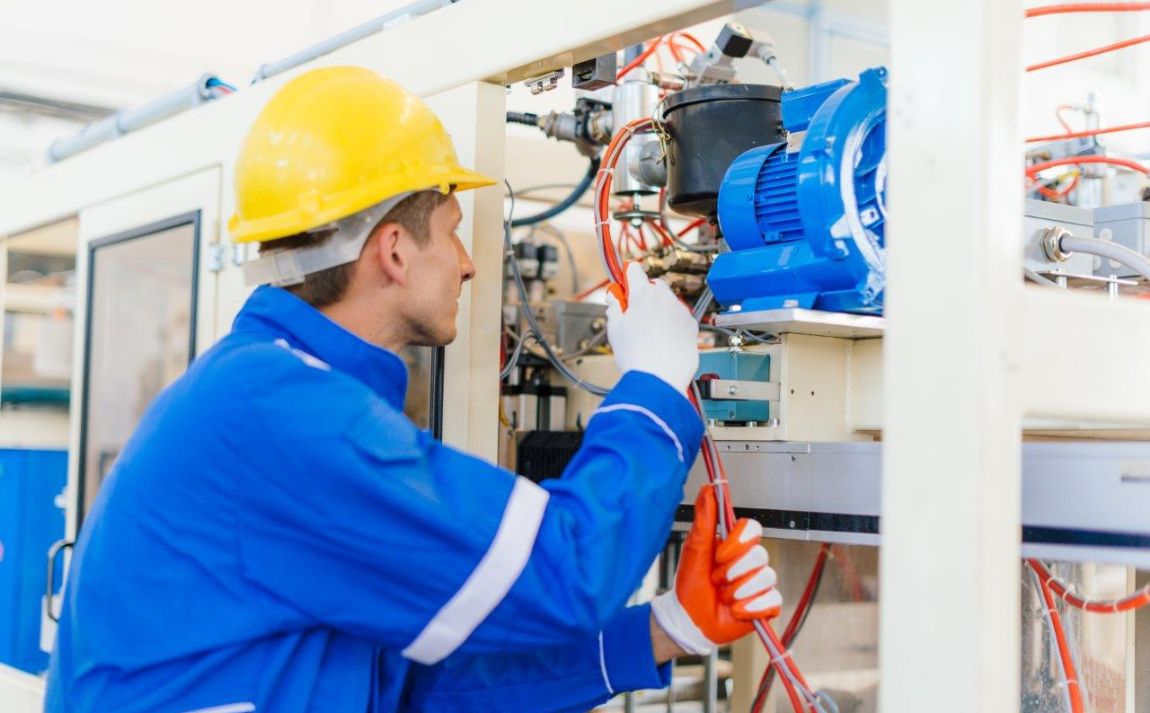
Thermoplastic elastomers (TPE), sometimes referred to as thermoplastic rubbers, are a class of polymers (usually a plastic and a rubber) which consist of materials with both thermoplastic (like PVC) and elastomeric (like rubber) properties.
Polymers can be divided into two categories, Thermoplastic and Thermoset.
Thermoplastic polymers flow (becomes soft and change shape) at elevated temperatures and once shaped can be reheated and reshaped as many times as desired. These materials are relatively easy to use in manufacturing processes both by injection moulding or extrusion.
Thermoset polymers once shaped will no longer melt or flow on reheating. The polymerisation process results in strong network bonds (i.e. cross-linking) which are facilitated by the application of heat and pressure during shaping. These strong bonds keep the material from re-melting. When reheated, to normal cable temperatures, say 90°C, even if higher temperature, say 110°C, there will be no change of shape.
Increasing temperature further, there can be charring and burning but no melting.
As such thermosetting materials cannot be re-cycled. Most elastomer materials used in cable manufacture are thermoset type and the cross-linking process is a critical structural factor which contributes to impart the materials high elastic properties.
TPE materials show advantages typical to both the elastomer materials and thermoplastic materials. In fact, TPE is commonly used to make suspension bushings for automotive performance applications because of its
greater resistance to deformation when compared to regular rubber bushings.
To qualify a polymer as a TPE, a material must have the following three essential characteristics:
- 1. The ability to be stretched to moderate elongations and, upon the removal of stress, return to something close to its original shape (so cable is easy to bend)
- 2. Can be processed as a melt at elevated temperature (so cable is easy to manufacture)
- 3. Absence of significant creep (so cable is dimensionally more stable)
TPE materials have the potential to be recyclable since they can be moulded, extruded and reused like plastics, but they have typical elastic properties of elastomers which are not recyclable owing to their thermosetting characteristics. TPE materials also require little or no compounding, with no need to add reinforcing agents, stabilizers or cure systems and hence can be processed on a simple plastic extrusion line. They also has the advantage of being relatively cheap in price when compared to the traditional commonly used elastomer materials.
The Olex TPE sheathing material, as used in the Olex-Flexs ‘Versolex®’ range of cables, is tough and durable, is resistant to abrasion, cut, crush and flex cracking while still being smooth and highly flexible. The material withstands both hot and cold environments, sustaining the mechanical performance properties from -40°C to 90°C. Additionally, the material has excellent resistance against the effects of UV, ozone, water, and a range of common oils, fuels, solvents, acids and alkaline chemicals. Cables sheathed with this material pass the flame propagation tests of AS/NZS 1660.5.6 and IEC 60332.1.
Our websites
Select your country to find our products and solutions
-
Africa
- Africa
- Ghana
- Ivory Coast
- Morocco
- North West Africa
- Americas
- Asia
- Europe
- Oceania