- Products
- Market Solutions & Services
- Insight
- Tools & Resources
- About Nexans Australia
- Search
- Contact us
- Compare
- Sign in
Common issues associated with PVC insulated and sheathed cables
Oct 27, 2021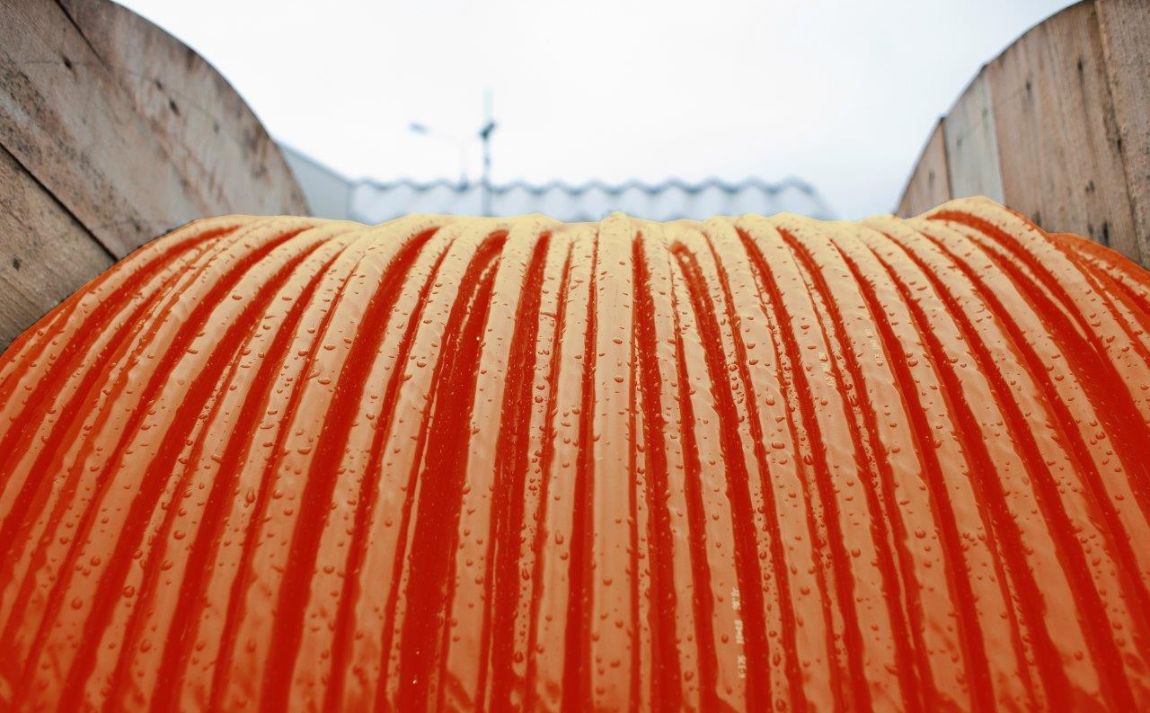
Green Goo
Also known as “Green Slime”, this phenomenon is characterised by the appearance of a sticky green exudate leaking out of PVC-insulated wiring at locations such as switches, hot points and light fittings. It is a common occurrence in both Australia and New Zealand.
The green goo problem is predominantly associated with older (25+ years) TPS-type cables operating in a warm environment. The exudate comprises a plasticiser that has migrated out of the PVC insulation, coloured due to reaction with the copper conductor, and that has subsequently travelled - by capillary action and/or gravity – along the conductor to emerge at a termination point.
Due to its stickiness and unsightly colour, the goo has a high nuisance value, however it poses no significant health hazard. It may be cleaned from surfaces by wiping with a rag soaked in a petroleum- or alcohol-based
solvent (such as meths).
The long-term consequence of the exudate is that it represents a de-plasticising of the insulation, meaning that as the process continues, the PVC will eventually become brittle, and crack.
TPS Cables in Polystyrene Thermal Insulation
With the increasing use of polystyrene block insulation in houses and caravans, it is important to explain the potential problem that arises when PVC sheathed and insulated cables come into direct contact with this material.
The plasticiser that is added to PVC to make it flexible, has a tendency to migrate out of the PVC and into materials with which it is in contact, particularly where those materials – such as polystyrene and polyurethane - have a great affinity for the plasticiser. This will lead to the PVC's becoming progressively harder and more brittle, while in contrast the polystyrene will appear to “melt” as it absorbs the plasticiser.
The rate of migration is dependent upon the relative thickness of the materials, the temperature, and the amount of surface area in direct contact. Accordingly, the rate of deterioration of the PVC cable can vary considerably under different circumstances.
To mitigate the problem it is recommended that the amount of direct contact between the cable and the polystyrene be reduced as much as possible. Effective ways of achieving this include positioning the cable with an air gap between the sheath and the polystyrene, or installing the cable within a rigid PVC or PE conduit.
Our websites
Select your country to find our products and solutions
-
Africa
- Africa
- Ghana
- Ivory Coast
- Morocco
- North West Africa
- Americas
- Asia
- Europe
- Oceania